在現代電子產品開發中,PCB不僅承載信號和電源分配,還直接影響制造成本。合理的元件布局能顯著降低鉆孔、銅耗、層數和裝配成本,為企業節約采購與生產開支。本文將從實用角度出發,分享多項可落地的優化策略,幫助您在設計階段“防患于未然”。
1. 了解成本的主要驅動因素
- 過孔與孔徑:每個過孔都會增加加工工序,微孔(<10?mil)成本更高。適當放大孔徑可減少工具費用與打樣失敗率。
- 板層數量:板層越多,材料和工藝成本呈幾何級數上升。盡量在保證信號完整性的前提下,控制在2–4層以內。
- 走線長度與銅耗:更長的走線意味著更多銅箔和更復雜的布線工序,也會延長生產周期。
> “增加小孔尺寸(如從8?mil到10?mil)以及減少板層數,是快速接近10%成本降低的常見手段”
2. 縮短信號線與加強分區布局
- 分區布局:將高頻、模擬與數字電路分區布局,不僅有助于信號完整性,也能縮短不同模塊之間的連線。
- 最短路徑優先:在布局階段優先選取最短連接路徑,減少轉角與過孔,既提升電氣性能,又降低材料與工時成本。
> “通過優化元件的擺放位置和信號線走向,可以減少線路長度,降低EMI干擾,同時節省材料與生產時間”
3. 減少過孔數量與合理設置孔徑
- 批量化孔徑:在設計規則中統一采用常用加工孔徑(10?mil以上),避免專用微孔。
- 過孔配合走線:對走線密集區域,可使用盲孔/埋孔工藝,但要嚴格評估成本增量。
> “優化PCB布局時,應考慮孔徑、通孔數量與間距,減少非必要的鉆孔與特種工藝”
4. 標準化元件封裝與BOM優化
- 常見封裝尺寸:優先使用0603、0805等主流SMT封裝,降低供貨與貼裝成本。
- 統一元件型號:同一功能可采用雙足跡(dual-footprint)或通用元件,以應對物料短缺且減少更換頻率。
- 完整BOM管理:在設計階段與供應鏈團隊溝通,鎖定性價比高且穩定供貨的零件。
> “選擇標準封裝、遵循DFM(Design for Manufacturability)原則,可簡化供應鏈并節省裝配費用”
5. DFM原則與制造可行性
- 對齊網格與組件方向:將所有SMT元件盡量同向排列,減少貼片來回拾放時間。
- 元件集中一側:將所有表面貼裝元件集中在PCB一側,降低返修與質檢成本。
- 預留測試點:合理布局測試點與探針孔,提高測試效率,減少返工。
> “確保將SMT元件放置在PCB的一側,并提供明確標記,可顯著降低裝配線的調試和返工成本”
6. 與制造商的協同與反饋迭代
- DFM評審:在定稿前組織DFM評審會,邀請PCB制造與SMT裝配商,對可行性與成本風險進行提前論證。
- 快速樣板驗證:在小批量階段進行驗證樣板,與制造商溝通,及時調整不合理的布局與工藝參數。
> “與可靠的制造合作伙伴保持緊密溝通,是降低PCB生產與裝配成本的關鍵一環”
總結
通過以上六大策略,您可以在PCB設計階段從源頭控制成本——從合理分區、最短走線到標準化封裝、DFM評審,每一步都能為后續制造與裝配節省成本與時間。宏力捷電子擁有豐富的多層、高精密/BGA封裝及盲埋孔PCB設計經驗,歡迎隨時咨詢,共同實現高效低成本的PCB解決方案。
深圳宏力捷推薦服務:PCB設計打樣 | PCB抄板打樣 | PCB打樣&批量生產 | PCBA代工代料
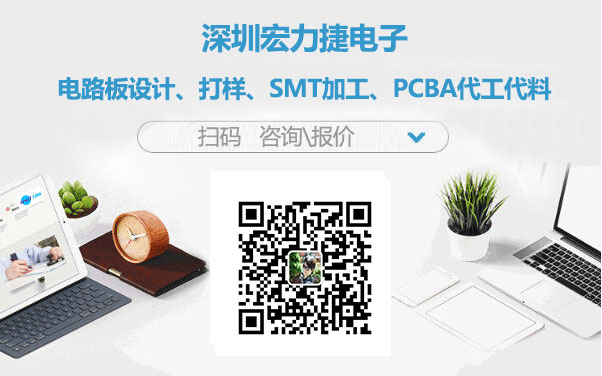